Decarbonizing Holcim with alternative fuels
At Holcim, we take a science-driven approach to become a net-zero company and have upgraded our targets to be in line with the 1.5°C framework.
Replacing fossil fuels with alternative fuels, such as biomass and other materials at the end of their life, is one of the key levers of our net-zero journey. We continuously and systematically innovate to accelerate the use of alternative fuels in our cement sites, with some plants in Europe already running at an almost 100% substitution rate.
The use of alternative fuels is decreasing cement carbon intensity while contributing to a more circular economy and reducing reliance on fossil fuels all at the same time.
Alternative fuels reduce the carbon intensity of cement and divert waste from incineration or landfill
European cement plants lead the way with some at nearly 100% alternative fuels
Next-generation technologies increase the substitution rate
Alternative fuels reduce the carbon intensity of cement, and more
Clinker, the main ingredient of cement, is produced in a kiln in a process that requires thermal energy. Kilns are usually heated by fossil fuels, and the combustion of these fuels produces about 40% of cement’s CO2 emissions.
To reduce the carbon intensity of our cement, at Holcim we replace fossil fuels with alternative fuels, including biomass and other sources of non-recyclable waste. In 2022, alternative fuels represented 28% of Holcim’s thermal energy demand for clinker production.
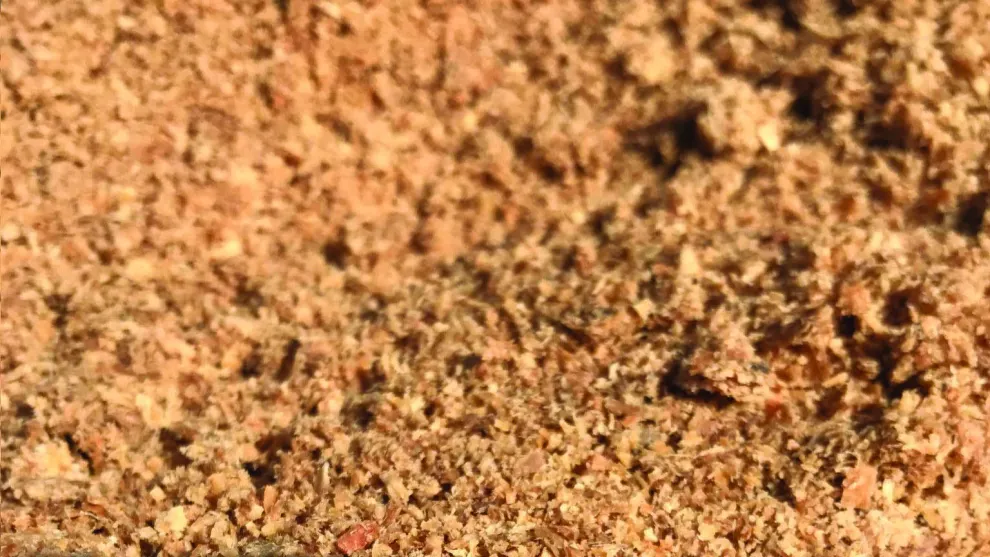
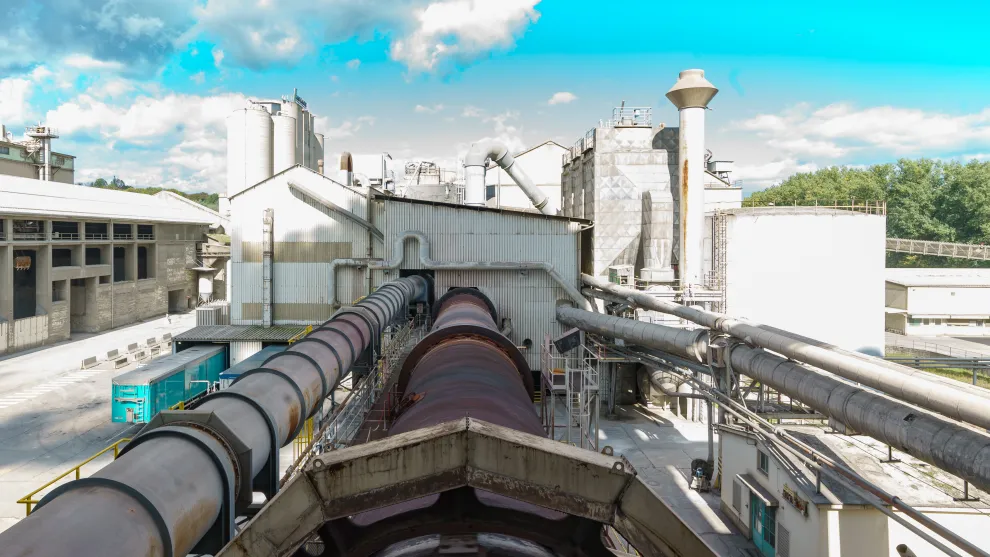
To increase the substitution rate of fossil fuels with alternative fuels, we are constantly investing in state-of-the-art technologies. As part of our net-zero roadmap, we aim to increase our thermal substitution rate to 50% by 2030 and reach over 70% by 2050.
By substituting traditional fuels with alternative fuels in our cement plants, we solve several problems at once: we reduce the reliance on fossil fuels, we lower the carbon intensity of our cement, and we offer a highly safe and ecological solution to waste at the end of its life, applying the most stringent international standards of waste management.
What is the thermal substitution rate (TSR)?
Proportion of cement kiln thermal energy provided by alternative fuels including biomass and other sources of non-recyclable waste
The plants leading the way
In line with the European Union waste policy, aiming to contribute to the circular economy by extracting resources from waste as much as possible, many of Holcim’s European plants source over 80% of their thermal energy from alternative fuels. Some of our sites, such as the ones in Austria and the Czech Republic, are operating at close to 100% alternative fuels.
Beyond Europe, at the forefront of waste management systems, we are making progress in countries where these are starting to develop. In Egypt, for example, we already operate with 20% alternative fuels and are on our way to increase this in the near future, all while contributing to a more circular economy in the country.
Next-generation technologies to increase alternative fuel usage
Our Plants of Tomorrow initiative, one of the largest Industry 4.0 programs in the sector, brings together a range of innovations aimed at improving the performance, circularity and carbon intensity of our cement plants.
One of the smart solutions deployed by this program is near-infrared spectroscopy, a digital online control technology, which can be used to analyze alternative fuel properties during the process of feeding the kiln, eliminating quality variations and allowing for an optimal fuel mix. This solution enables maximizing the use of alternative fuels and therefore the reduction of CO2 emissions.
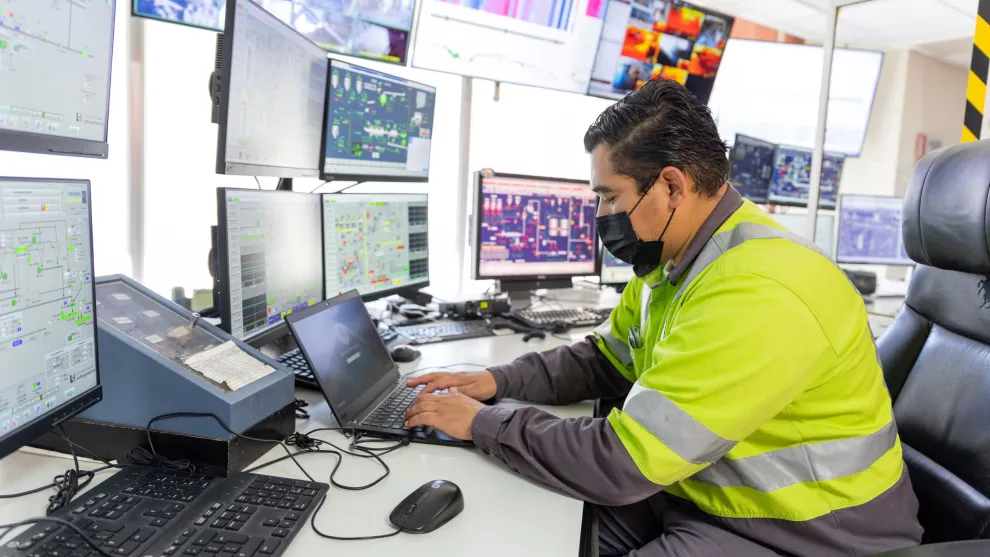